A dusty affair - from rapid prototyping to additive serial production
Additive manufacturing already offers many new possibilities today. Overnight, hand samples, prototypes and functional elements are created from different materials, such as plastic, metal and even ceramics. In the past, generative manufacturing was mainly used for "rapid prototyping". “Direct manufacturing" and "direct tooling" are bringing new requirements to additive manufacturing. Protiq GmbH describes the special challenges for system technology and material for series production from the user's point of view.
Direct Manufacturing
In the case of "direct manufacturing", end products are produced directly and additively without the use of tools. The product and its application area therefore define the requirements for material and manufacturing technology. For example, the electronics industry has high requirements for the electrical properties or flammability of products.

From a total cost of ownership (TCO) perspective, additively manufactured, improved molds can drastically reduce the manufacturing costs of end products. These tools respectively injection molds offer the potential to save weight and shorten process and cycle time. In the production of injection molds, the mechanical parameters such as strength, ductility or surface hardness are of primary importance.
"Materials that fit the requirements are needed to enable mass production with additive manufacturing."
The mentioned application examples for additive manufacturing show that the currently existing material selection for additive manufacturing is mostly insufficient for these applications. The qualification of new materials, with tailored properties, is a fundamental prerequisite for the future, broad and economic use of additive manufacturing in industrial production.

Laser sintering with high material requirements
In plastic laser sintering, the majority of products are built up from the base material PA12, with or without fillers. However, many industries require engineering plastics that meet the requirements for the end products. Of particular importance are the materials polyamide 6 (PA6), polyamide 6.6 (PA6.6), polybutylene terephthalate (PBT) or thermoplastic polyurethane (TPU) . The standard plastic polypropylene (PP) is also very widely used. The existing system technology was originally developed for the production of individual prototypes and only allows the processing of these technically relevant plastics to a limited extent. From the user's point of view, further development of 3D printing technologies is necessary in order to meet the increased requirements of direct production.
The range of materials is also very limited in the metallic sector. Copper alloys are of great importance for conductive structures and elements. However, processing highly conductive copper by generative methods presents a special challenge. Like a mirror, the red material reflects the wavelength of the classic red laser, so that most of the laser energy is reflected and does not cause the material to fuse, as desired.
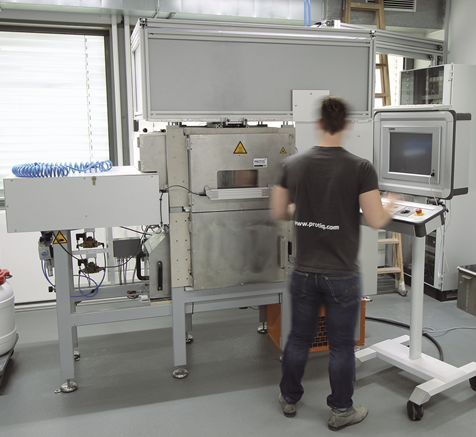
A newly developed machine technology enables the processing of metals such as highly conductive copper, zinc, brass and also engineering plastics such as PA6 and TPU.
Process modifications provide a solution for this, meaning that it is already possible today to additively process highly conductive copper as well. This adapted laser melting process also enables the processing of zinc and brass. While zinc can be used, for example, to supplement conventional zinc die casting product families with small quantities, the processing of brass offers new degrees of freedom for the jewelry or fittings industry. The processing of high-strength steels also offers great potential. Technologically, this requires higher process temperatures. Together with renowned research institutes in North Rhine-Westphalia and heater manufacturers, Protiq GmbH is already working on new technical solutions for this, so that typical tool steels, such as a 1.2343, will also supplement the range of materials in the near future.
„High tech meets stone age“
Direct manufacturing requires the automation and interlinking of system technology with conventional manufacturing technologies.
The actual production process in additive manufacturing is highly developed and fully automated, but the upstream and downstream processes usually require a great deal of manual effort: components are manually cleaned of adhering powder, and the residual powder is manually reprocessed in order to feed it back into the process. Even the setup of the equipment is done manually, so that in single-shift operation, it is sometimes not possible to achieve optimum equipment utilization. The latest generation of systems has interfaces, so that increasing automation is becoming apparent along the process chain from 3D data handling to work preparation (positioning and support generation), processing and post-processing, and packaging. In particular, the unresolved issues in automation technology offer the opportunity for domestic special machine builders to tap into the attractive market of additive manufacturing.
"Only digital networking along the vertical and horizontal value creation processes enables lean, flexible production of customized series products."
Additive manufacturing enables production within a few hours. The speed should not be slowed down by long, conventional ordering processes. Digital data handling is the prerequisite for automated vertical integration - from the customer to production. The first Internet platforms streamline the ordering process and at the same time enable linking with established SAP systems. This includes 3D model analysis incl. 3D data repair, online pricing for the offered processes and materials incl. configuration, scaling and post-processing, the selection of the appropriate logistics service as well as the payment provider up to the ordering of the digital shopping carts.
More News
Are your 3D files ready?
Just upload your data. All files are automatically checked and optimized for printing.