Online-based topology optimization in 3D printing
Maximum functionality with low material consumption and weight
Additive manufacturing opens up new possibilities for improving the geometry of components as part of product development. Compared to conventional manufacturing methods, it is not limited by process-related production constraints. On the Protiq platform, 3D models can be optimized online quickly and easily.
Until now, designers and engineers have always had to take process-related limitations into account during product development. In additive manufacturing, however, a component is not machined out of a block of material but built up layer by layer from a formless starting material. In this way, product developers can focus entirely on the functionality of an object when designing it. Two-dimensional layer-by-layer construction in 3D printing can therefore solve the three-dimensional challenges and problems associated with conventional processing. Based on topology optimization, basic shapes can be generated taking into account defined boundary constraints and stress restrictions in such a way that they combine maximum performance characteristics with low material consumption and weight. The combination of topology optimization with additive manufacturing processes and innovative materials thus offers designers new opportunities to rethink the shaping and the associated functional scope of products.

Industries for which weight reduction plays a major role are among those benefiting from the force-flow-oriented design. These include, for example, the automotive industry and the aerospace industry. Topology optimization is a computer-based calculation method that can design mechanically loaded component structures in such a way that the greatest possible stiffness is achieved with minimum material input. In this optimization process, only those areas of a component are generated that are required for the necessary force flow and stability. This results in complex structures that cannot be realized, or only to a limited extent, using conventional production processes and their manufacturing restrictions.
Intuitive user interface of topology optimization
Demand-specific production of industrial components creates functional added value for customers, while suppliers differentiate themselves from the competition with innovative solutions. Web-based configurators are available on the Protiq platform, enabling customers to adapt individual components made of plastic or metal in just a few minutes and order them directly. This gives interested customers the opportunity to intuitively and quickly generate models that fully meet their specific requirements, without any special knowledge of CAD design. In this context, the platform offers another option to meet the customers' wishes as well as the market demand: Protiq has implemented here an easy-to-use software to realize a topology optimization of components.

In direct comparison, the conventional improvement of component design requires an extensive and detailed understanding concerning the usage of common application software. This solution on the Protiq platform makes topology optimization comprehensible and conclusive even for non-professionals. To this end, the intuitive user interface allows complete traceability of the individual steps at any time, as the customer is guided through the inputs with a variety of explaining and instructional texts. In addition, the entire topology optimization process can be run through and tested in advance using sample components in combination with an introductory tutorial.
Directly printable 3D model
So how exactly does topology optimization work? First, the customer defines the maximum design area available for designing the optimized geometry. In this context, there is the option of defining an unrestricted space so that optimized structures can be generated wherever the force flow requires it. Alternatively, the design space can be limited so that the automated design and improvement process is performed in a predefined space. This restriction proves useful when adjacent components within a subassembly will limit the available space. An example is the cramped engine compartment in a passenger car. For such a limitation, the maximum design space must be created and uploaded.
Once the design space has been defined, various load cases have to be considered, which the structure has to withstand in the application. A load case describes a situation in which different forces can act simultaneously, and which includes existing bearing elements. Of course, each component is subject to different force conditions. A model can therefore be influenced by numerous load cases. The software analyzes the applied forces on the model considering the connection points, which are also called bearing conditions. All areas that are not subject to any load and have no other use are automatically removed from the 3D model by the software. The result reminds of bionic structures and combines high functionality with low weight as well as material costs. The 3D model generated in this way is directly printable, which means that no manual follow-up processes are required to achieve the optimization goal. "In the future, the components will also be automatically optimized for additive manufacturing. This is nothing less than a revolution," explains Dr. Ralf Gärtner, Managing Director of Protiq GmbH.
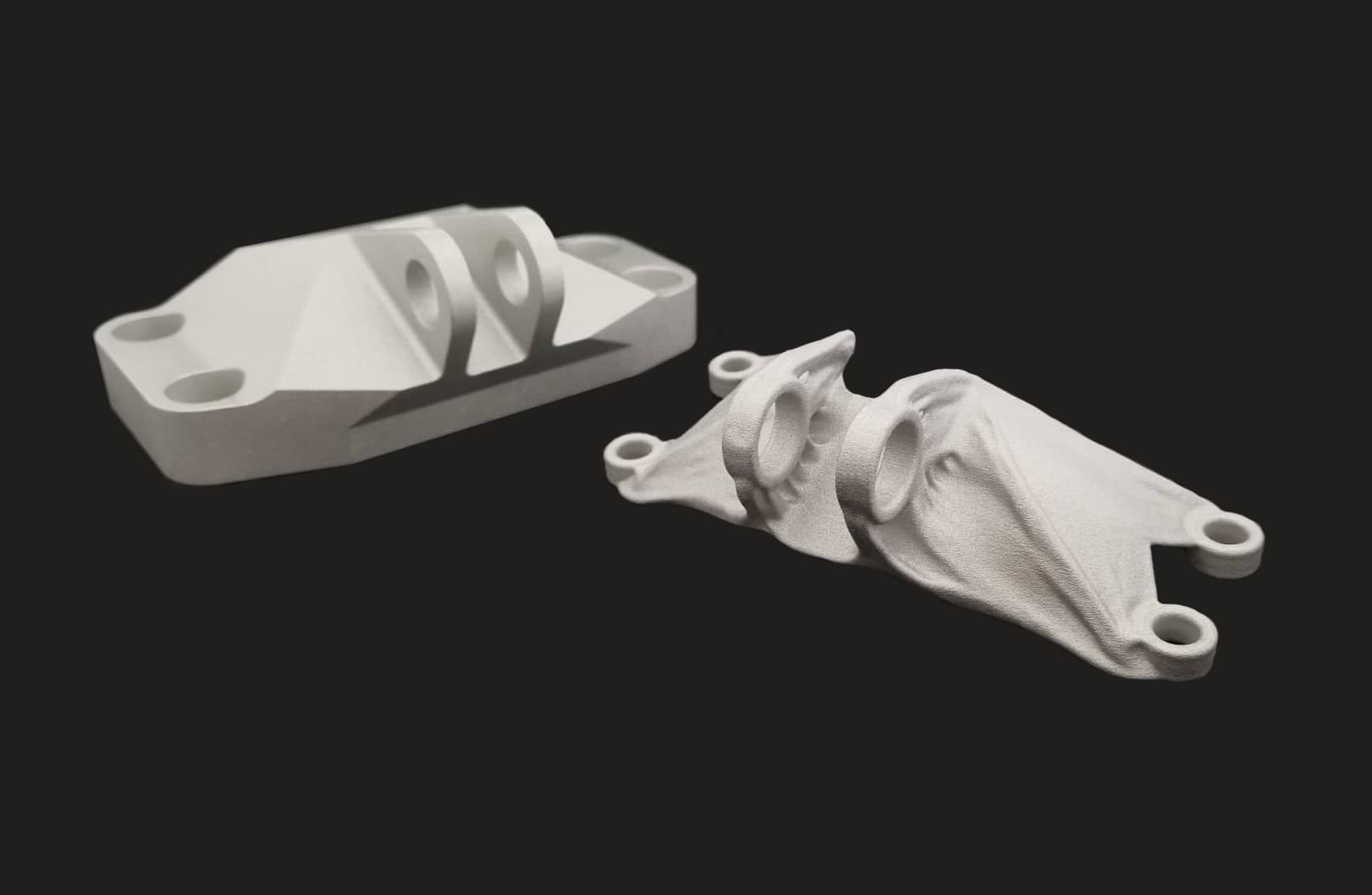
Consistent live pricing
The online tool provided on the Protiq platform makes topology optimization much easier and faster. Previously, the process required extensive knowledge of using specialized application software, so even simple use cases often took days or even weeks to complete. With online-based topology optimization, long waiting times are now a thing of the past, because Protiq software does not require any specialized knowledge to improve a 3D model, but only a few mouse clicks. This significantly reduces not only the amount of material required, but also the time it takes - while maintaining the high quality and performance of the products.
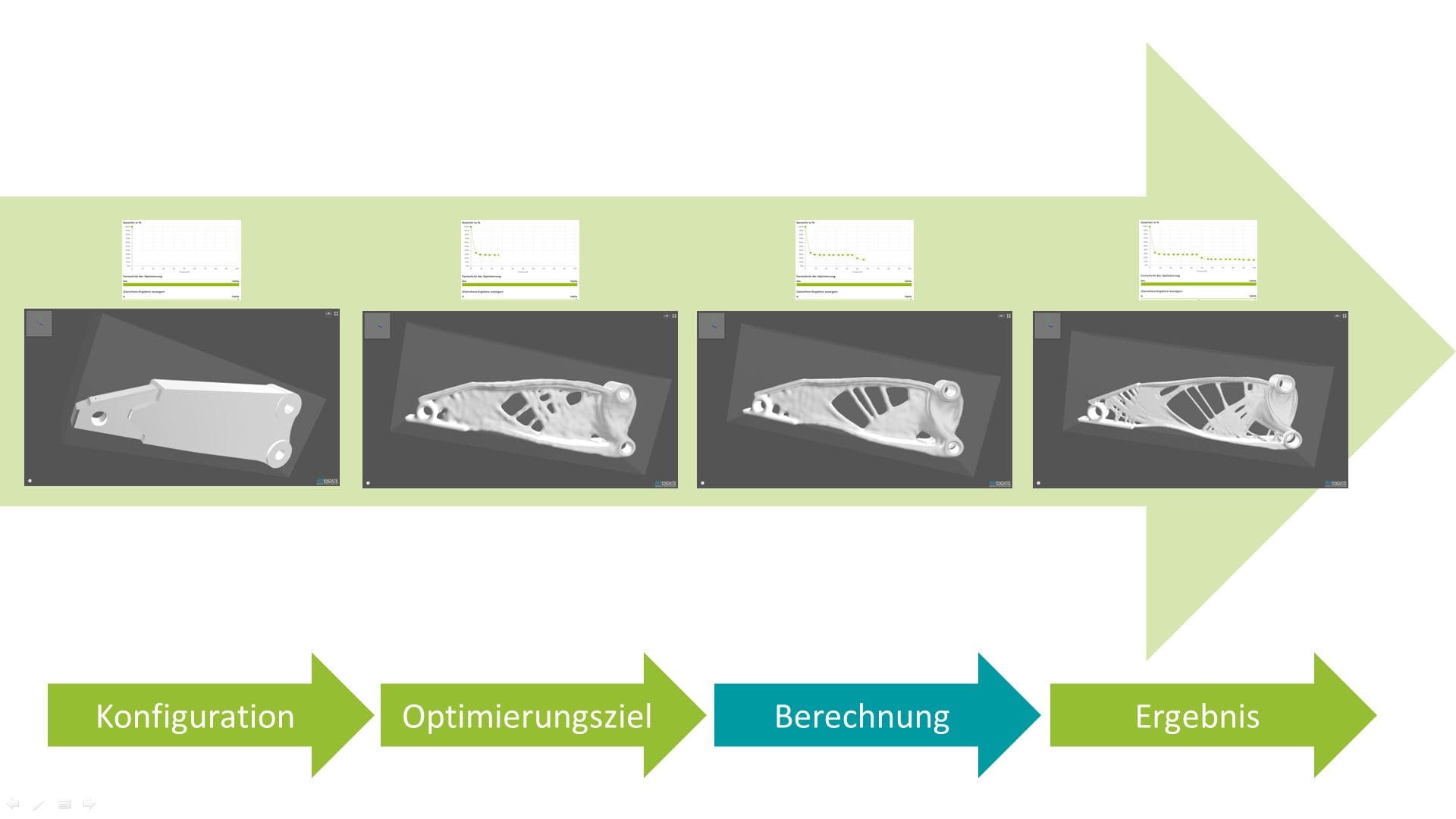
Once the optimized 3D model has been generated with this software tool, it can be saved as a project design, purchased as a CAD model, or ordered directly from Protiq. The component is then manufactured in industrial 3D printing by selective laser melting or laser sintering. A particularly charming feature is the continuous live pricing, which is constantly updated throughout the project. So, the customer doesn't just get an improved design. At the same time, production costs can be significantly reduced through additive manufacturing, because "every printed gram costs", as Dr. Ralf Gärtner explains.
More News
Are your 3D files ready?
Just upload your data. All files are automatically checked and optimized for printing.